All Events /
MAPP Lecture Series - Dr Stefania Soldini
The next MAPP Lecture 'Connected Everything Feasibility Study on Manufacturing of 3D-printed morphing origami solar sails for next generation of CubeSat' will be delivered by Dr Stefania Soldini, Lecturer in Space Engineering at the University of Liverpool, on Thursday 9 December, 2pm - 3.30pm, via Zoom.
To access the online event, please follow the link below:
https://liverpool-ac-uk.zoom.us/j/99385042058?pwd=czNRR2kxM0RUdWtKZFgwV3Yza3Uzdz09
Meeting ID: 993 8504 2058
Passcode: &68tzC.?).
Dr Soldini is Lecturer in Space Engineering at the University of Liverpool, UK since 2019. Dr Soldini is PI of a feasibility study in manufacturing of origami solar sails funded by the Connecting Everything Network plus/EPSRC. Dr Soldini is core team member of ESA/HERA, NASA/DART and JAXA/Hayabusa2 missions as astrodynamics Co-I. She was the PI of the "Hayabusa 2" superior solar conjunction mission operations in late 2018. She worked at the JAXA’s Institute of Space and Astronautical Science (ISAS) from 2016 until 2019 after completing a one-year JSPS Post Doc Research Fellowship at the same institution. Dr Soldini received her Ph.D. in October 2016 from the Astronautical Research Group of the University of Southampton, UK. Her research interests are in astrodynamics, Guidance, Navigation &Control (GNC) for asteroids proximity operations, ejecta particles dynamics, planetary defence, solar sail technology, origami robotics and additive manufacturing.
Abstract
Conventional spacecraft design comprises of a central spacecraft bus that mounts multiple deployable structures (e.g. antennas and solar arrays). Deployables are used to minimise the packed volume in the launch vehicle and to provide on-orbit configurations which aim to extend the surface area of the spacecraft. These devices are generally large structures deployed in-space utilising origami-based designs. However, all such large devices are currently designed to maintain a fixed-shape once deployed and a single spacecraft usually mounts multiple deployables for different purposes. In this talk, a self-reconfiguring OrigamiSat concept is presented. A shape-changing spacecraft could open to a new paradigm in spacecraft design where a “flat” OrigamiSat could be multi-operational and achieve several shape configurations to perform different functions. The reconfiguration of the proposed OrigamiSat is triggered by combining the effect of 4D material (i.e. origami’s edges) and changes in the local surface optical properties (i.e. origami’s facets) to harness the solar radiation pressure acceleration. Our approach uses the principle of solar sailing to enhance the effect of the Sun radiation to generate momentum on the aluminised Kapton origami surface by transitioning from mirror-like to opaque optical properties of each individual facet. Numerical simulations have demonstrated that local changes in the optical properties can trigger reconfiguration. A minimum of 1-meter edge size facet is required for a thick-origami with thin Al-Kapton film to generate enough forces from the Sun radiation. The thick-origami pattern is 3D-printed directly on a thin Al-Kapton film (the solar sail substrate which is highly reflective). An elastic filament (thermoplastic polyurethane TPU) showed best performance when printing directly on the Kapton and the Acrylonitrile Butadiene Styrene with carbon fiber reinforcement (ABS/cc) is added to augment the origami mechanical properties. The 4D material (shape memory polymer) is integrated only at specific edges to achieve self-deployment by applying heat. Two different folding mechanisms were studied: (1) the cartilage-like origami pattern, where the hinge is made combining the TPU and the 4D material which make the mounts or valleys fully stretchable, and (2) the mechanical origami pattern, where simple hinges are made solely of ABS/cc. Numerical simulations have demonstrated that the cartilage-like hinge is the most suitable design for light-weight reconfigurable OrigamiSat when using the solar radiation pressure acceleration. We have used build-in electric board to heat up the 4D material and trigger the folding. We envisage imbedding the heat wire within the 4D hinge in the future.
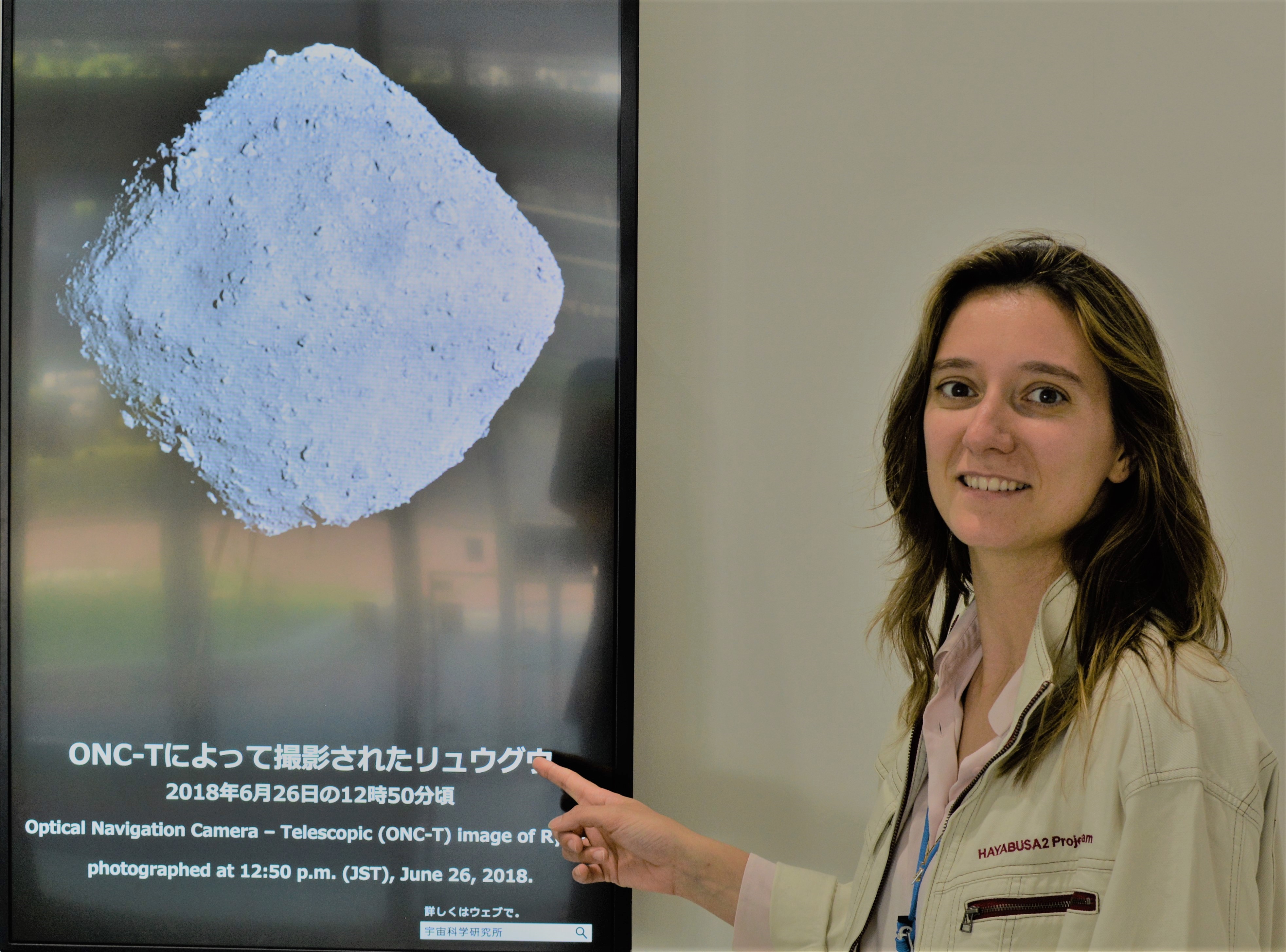